Plastic extrusion for tubing, profiles, and custom shapes
Plastic extrusion for tubing, profiles, and custom shapes
Blog Article
A Comprehensive Overview to the Refine and Advantages of Plastic Extrusion
In the substantial world of manufacturing, plastic extrusion emerges as a crucial and extremely effective procedure. Translating raw plastic into continuous profiles, it caters to a plethora of markets with its remarkable adaptability.
Recognizing the Basics of Plastic Extrusion
While it might show up complicated at very first glance, the process of plastic extrusion is fundamentally simple - plastic extrusion. It is a high-volume manufacturing technique in which raw plastic is thawed and formed right into a continual profile. The procedure begins with the feeding of plastic material, in the type of granules, powders, or pellets, right into a warmed barrel. The plastic is then thawed utilizing a mix of warmth and shear, used by a turning screw. Once the molten plastic gets to the end of the barrel, it is compelled via a small opening called a die, forming it right into a desired form. The shaped plastic is after that cooled, strengthened, and reduced into desired lengths, finishing the process.
The Technical Process of Plastic Extrusion Explained
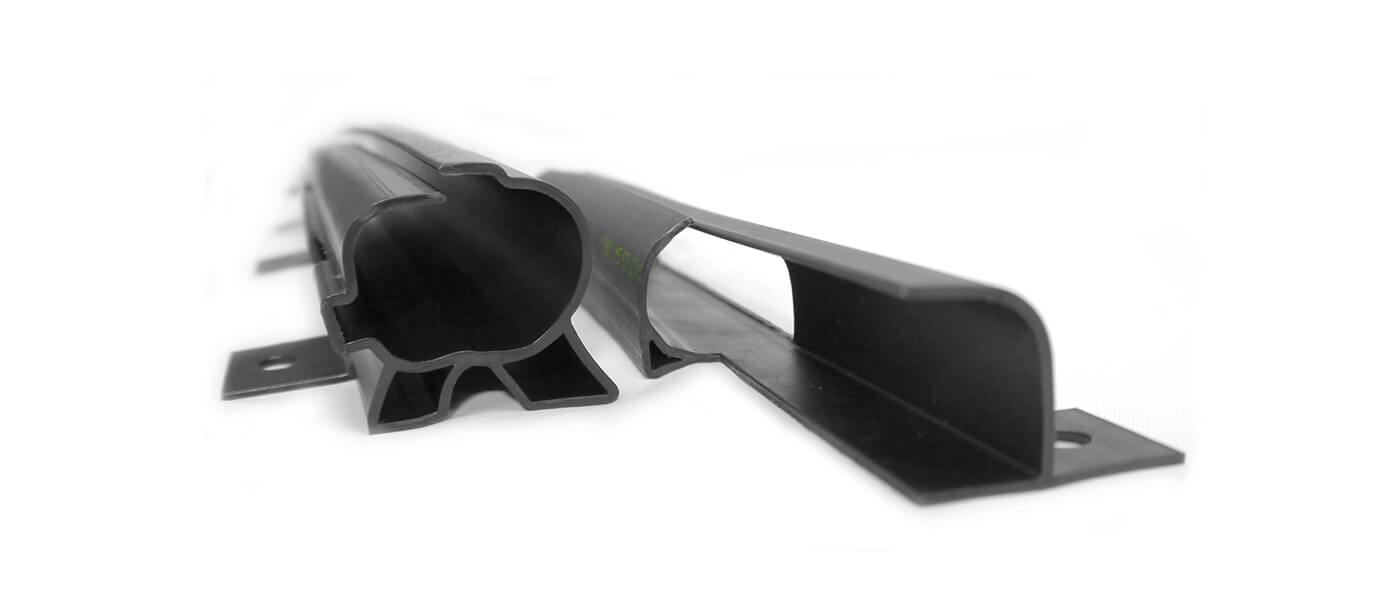
Sorts Of Plastic Suitable for Extrusion
The choice of the appropriate type of plastic is a crucial aspect of the extrusion procedure. Different plastics offer special residential or commercial properties, making them much more fit to particular applications. Polyethylene, for instance, is commonly made use of because of its reduced cost and simple formability. It uses exceptional resistance to chemicals and wetness, making it excellent for items like tubing and containers. Likewise, polypropylene is another prominent choice due to its high melting point and resistance to exhaustion. For even more robust applications, polystyrene and PVC (polyvinyl chloride) are often chosen for their toughness and durability. These are typical alternatives, the selection ultimately depends on the particular demands of the item being created. So, comprehending these plastic types can significantly improve the extrusion procedure.
Comparing Plastic Extrusion to Other Plastic Forming Techniques
Comprehending the kinds of plastic suitable for extrusion leads the way for a broader discussion on just how plastic extrusion stacks up against other plastic forming techniques. These consist of shot molding, impact molding, and thermoforming. Each technique has its one-of-a-kind uses and benefits. Shot molding, for instance, is excellent for creating elaborate parts, while impact molding is excellent for hollow objects like containers. Thermoforming excels at developing large or superficial components. Plastic extrusion is unrivaled when it comes to creating continual profiles, such as pipes, gaskets, and seals. It likewise enables a constant cross-section along the size of the item. Thus, the option of technique mostly depends on the end-product demands and requirements.
Secret Benefits of Plastic Extrusion in Manufacturing
In the world of manufacturing, plastic extrusion offers lots of significant benefits. One significant advantage is the cost-effectiveness of the process, which makes it a financially enticing production technique. In addition, this technique provides superior product flexibility and enhanced manufacturing rate, thereby enhancing total manufacturing efficiency.
Economical Production Method
Plastic extrusion hop over to these guys jumps to the leading edge as a cost-effective production approach in production. This procedure sticks out for its capability to generate high volumes of product quickly and successfully, providing makers with significant financial savings. The main expense benefit is the ability to use much less pricey basic materials. Extrusion utilizes thermoplastic materials, which are much less expensive contrasted to ceramics or metals. Further, the extrusion procedure itself is reasonably straightforward, minimizing labor prices. In addition, plastic extrusion needs less power than standard production techniques, here are the findings adding to lower operational prices. The process additionally minimizes waste, as any malfunctioning or excess products can be recycled and reused, providing an additional layer of cost-effectiveness. On the whole, the monetary benefits make plastic extrusion a highly eye-catching choice in the production sector.

Superior Product Versatility
Beyond the cost-effectiveness of plastic extrusion, one more significant benefit in producing depend on its remarkable item versatility. This procedure permits for the creation of a wide range of products with varying sizes, forms, and styles, from easy plastic sheets to intricate profiles. The adaptability is credited to the extrusion die, which can be tailored to yield the wanted product style. This makes plastic extrusion an excellent remedy for industries that need customized plastic elements, such as vehicle, building and review construction, and product packaging. The capability to generate diverse products is not only useful in conference details market demands however likewise in making it possible for producers to explore brand-new item lines with very little capital expense. In essence, plastic extrusion's product versatility promotes development while enhancing operational effectiveness.
Enhanced Manufacturing Rate
A substantial advantage of plastic extrusion exists in its enhanced manufacturing rate. Few various other manufacturing processes can match the rate of plastic extrusion. Furthermore, the capacity to keep consistent high-speed manufacturing without compromising product high quality establishes plastic extrusion apart from various other methods.
Real-world Applications and Influences of Plastic Extrusion
In the realm of manufacturing, the method of plastic extrusion holds extensive value. This procedure is widely utilized in the manufacturing of a range of items, such as plastic tubing, home window structures, and climate removing. Therefore, it substantially influences fields like construction, packaging, and vehicle markets. Its impact prolongs to day-to-day products, from plastic bags to toothbrushes and disposable cutlery. The financial benefit of plastic extrusion, primarily its high-volume and cost-efficient output, has actually changed production. The environmental impact of plastic waste stays an issue. As a result, the sector is persistently pursuing advancements in recyclable and biodegradable materials, indicating a future where the advantages of plastic extrusion can be retained without endangering ecological sustainability.
Conclusion
To conclude, plastic extrusion is a reliable and very effective technique of changing basic materials right into diverse items. It offers countless benefits over various other plastic forming approaches, including cost-effectiveness, high result, marginal waste, and layout versatility. Its effect is profoundly felt in different sectors such as building, automotive, and consumer products, making it a pivotal procedure in today's manufacturing landscape.
Digging deeper into the technological procedure of plastic extrusion, it begins with the selection of the proper plastic product. As soon as cooled down, the plastic is cut right into the required sizes or wound onto reels if the product is a plastic movie or sheet - plastic extrusion. Comparing Plastic Extrusion to Other Plastic Forming Methods
Comprehending the kinds of plastic suitable for extrusion leads the means for a wider discussion on how plastic extrusion stacks up against other plastic creating methods. Few other manufacturing processes can match the rate of plastic extrusion.
Report this page